- Major milestone toward hybrid electric flight for commercial passenger air travel
- World’s first megawatt-class (high power) and multi-kilovolt (high voltage) hybrid electric system tested in altitude conditions
- Altitude integration test completed at NASA’s NEAT facility
- One MW could power more than 600 houses*
At the Farnborough International Airshow, GE announced it completed the world’s first test of a megawatt (MW)-class and multi-kilovolt (kV) hybrid electric propulsion system in altitude conditions that simulate single-aisle commercial flight.
This press release features multimedia. View the full release here: https://www.businesswire.com/news/home/20220719005415/en/
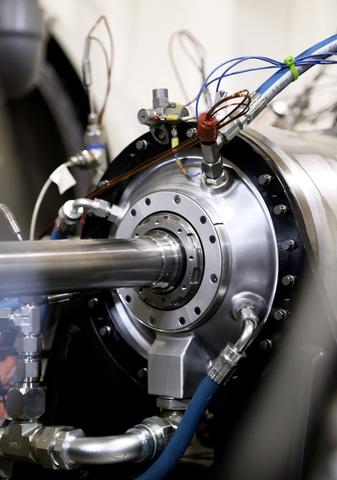
GE completes the world's first test of a megawatt (MW)-class and multi-kilovolt (kV) hybrid electric propulsion system in altitude conditions that simulate single-aisle commercial flight. (Photo: Business Wire)
The test of the high power, high voltage system — including electric motor/generators, power converters, power transmission and power control systems — successfully demonstrated performance and operation of the components in a replicated flight environment. This helps validate the architecture of the hybrid electric propulsion systems GE is developing. It’s also an important, necessary step in GE’s technology programs with NASA to develop a hybrid electric propulsion system for flight tests later this decade and for entry into service in the mid-2030s.
The altitude integration test of the system began in June 2021 and was completed earlier this year at NASA’s Electric Aircraft Testbed (NEAT) facility in Sandusky, Ohio. To represent the right and left engine side of an aircraft, two sets of a hybrid electric system were operated in conditions up to 45,000 feet, simulating the electrical loads required to help optimize the engines and propel and power an aircraft.
“We’re making aviation history by developing the technology to help make hybrid electric flight possible for everyday commercial air travel,” said Mohamed Ali, vice president and general manager of engineering for GE Aerospace.
“GE is proud to be a longstanding partner with NASA for development of new aviation technologies. Together, we just passed a key milestone by successfully concluding the world’s first test of a high power, high voltage hybrid electric system at altitude conditions. We appreciate the collaboration to make this possible. This is one of many milestones in our journey with NASA towards demonstrating a hybrid electric aircraft engine system for a more sustainable future of flight,” Ali said.
The NEAT facility where testing took place is a NASA reconfigurable testbed used to design, develop, assemble and test electric aircraft power systems.
“NASA’s unique NEAT facility is the only testing location capable of simultaneously providing both high-electric power and high-altitude conditions in an area large enough to fit an entire electric powertrain, and we are proud to see this test with GE come to a successful conclusion. This facility has become highly sought after by GE and others across the aviation community, and it is critical to supporting the agency’s goal of developing technologies that will enable and support future climate change adaptation initiatives,” said Bob Pearce, associate administrator for NASA’s Aeronautics Mission Research Directorate.
“At NEAT, we are able to test a high-voltage powertrain system in flight altitude conditions without leaving the ground, thereby reducing major safety risks in a timely manner. With the ground testing completed, we are now well positioned to move to the next phase of our agreement with GE, an actual electric aircraft flight demonstration,” Pearce added.
About the altitude integration test
Components were tested independently and as an integrated system. Additionally, multiple operational modes were evaluated, including power transfer from side to side, power assist to a simulated engine, and aircraft power generation. The implementation of energy storage was also simulated.
MWs measure electrical power and kVs measure the difference in electrical potential between two points, equivalent to the pressure used to drive fluid through a pipe. A kV-class system enables high efficiency and specific power. Successfully testing a kV system in altitude conditions is significant because the interaction of voltage and the environment is different at higher altitudes than on the ground. kV-class systems are significantly more difficult to manage at altitude.
What’s next for hybrid electric flight
Future tests will continue as part of the Electrified Powertrain Flight Demonstration (EPFD) project that was announced by NASA in September 2021, including testing of the hybrid electric system connected to GE’s CT7 turboprop engines. Eventually, this will lead to a flight test later this decade of the hybrid electric system on a CT7-powered Saab 340B plane.
Boeing is partnering with GE to support the flight tests for EPFD. Boeing and its subsidiary Aurora Flight Sciences is providing the aircraft, aircraft modification, aircraft integration and flight-testing services. That work includes nacelle manufacturing, flight deck interface design and software, aircraft-level performance analysis, and systems integration.
GE sustainability goals
More information on how GE is helping the aviation industry decarbonize, including a link to GE’s 2021 Sustainability Report, is available at www.GEAviation.com/Future-of-Flight. The recently released Sustainability Report outlines GE’s approach to achieving its 2050 net zero ambition for sold products, including guiding principles, progress to date and planned investments into new technology maturation.
Hybrid electric propulsion technologies can help reduce fuel usage, reduce CO2 emissions and optimize engine performance. Electrification technologies being developed by GE are also compatible with Sustainable Aviation Fuel, hydrogen, advanced engine architectures such as open fan, and new compact engine core designs.
*Calculated based on average annual electricity consumption for residential customers in the U.S. available from the U.S. Energy Information Administration.
ABOUT GE
GE Aviation, an operating unit of GE (NYSE: GE), is becoming GE Aerospace. The business is a world-leading provider of jet engines, components and systems for commercial and military aircraft with a global service network to support these offerings. With an installed base of 39,400 commercial and 26,200 military aircraft engines, the business is playing a vital role in shaping the future of flight.
View source version on businesswire.com: https://www.businesswire.com/news/home/20220719005415/en/
Contacts
Chelsey Levingston, GE Aviation
513-720-6458
chelsey.levingston@ge.com
Brian Newbacher, NASA’s Glenn Research Center
440-433-5644 (office)
216-469-9726 (mobile)
brian.t.newbacher@nasa.gov